Artikel Übersicht
Applikationen

An dieser Stelle möchten wir Ihnen mit einer Auswahl an Videos zum Pulverspritzgießen zum einen nochmals einen Einblick in den Prozess geben und zum anderen mögliche Applikationen vorstellen. Dazu werden wir Ihnen vorerst 2 verschiedene Werkzeugsysteme vorstellen. Zuerst ein Zweikomponentenwerkzeug des Werkzeugbauers Z-Werkzeugbau und in einem weiteren Video werden wir Ihnen die Mikrosystem 50 der Firma Wittmann Battenfeld mit einem Werkzeug der Firma Z-Werkzeugbau vorstellen. Alle vorgestellt Videos stellen den PIM Prozess da und wurden am IMF III des Forschungszentrums Karlsruhe GmbH im Rahmen der Forschungen zum SFB 499 erstellt.
Zweikomponentenspritzgießen von keramischen Feedstock
Mikrospritzgießen, neue Wege zur herstellung kleinster Bauteile
Neben den in den Videos vorgestellten Applikationen gibt es eine Vielzahl von Anwendungen im Bereich der Medzintechnik in der mittlerweile z.B. Brackets durch Pulverspritzgiessen hergestellt werden. Aber auch andere Applikationen werden durch das Pulverspritzgiessen gelöst. Wenn Sie auch mit Ihrem Beispiel dazu beitragen möchten diesen Unterpunkt zu Verbessen, treten Sie bitte mit uns in Kontakt.
Ofentechnik

Werkzeugtechnik

Wie auch im klassischen Spritzgießen wird auch im Pulverspritzgießen mit Mehrkavitätswerkzeugen gearbeitet. Dadurch ist es möglich sehr hohe Stückzahlen in einem Spritzgießzyklus herzustellen. Auch Mehrkomponentenwerkzeuge sind für das Pulverspritzgießen geeignet. Dabei kann zum Teil auch die Heißkanaltechnik Verwendung finden. Hier muss jedoch auch auf die Verschleißfestigkeit des verwendeten Heißkanals geachtet werden.
Maschinentechnik

Als Maschinenhersteller sind hier z.B. Arburg, Engel, Ferromatik Milacron und Wittmann Battenfeld zu nennen. Eine genauere Auflistung der Maschinenhersteller und ein Vergleich von Vor- und Nachteilen wird aktuell von uns erarbeitet. Wenn Sie weitere Informationen wünschen, treten Sie bitte mit uns in Kontakt.
Sintern

Beim Sintern werden über ein Wärmebehandlungsverfahren lose gebundene Pulveransammlungen in einen festen Verbund überführt. Im Detail bezeichnet das Sintern alle physikalischen Vorgänge zum vollständigen Verschmelzen der Pulverpartikel zu einem bis zu 100% dichten Bauteil.
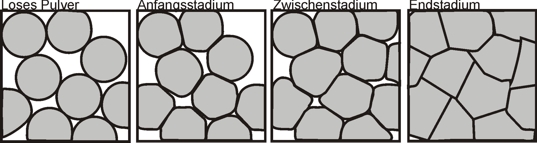
Beim Pulverspritzgießen wird dabei ein sogenanntes
dispersives System (Grünteil) beim Sintern in einen stabileren Zustand
und weniger porösen Körper überführt. Es wird bei keramischen und
metallischen Pulvern, wie auch bei Metalllegierungen verwendet. Das
Sintern beim Pulverspritzgiessen unterscheidet sich zum "normalen"
Sintervorgang prinzipiell nicht. Durch eine geeignete Temperaturführung
werden sehr gute Dichten bzw. Festigkeiten erreicht. Die Schwindung kann
zuvor berechnet werden und somit ist es möglich Bauteile gezielt
herzustellen. Der Antrieb der Sinterung, also des Zusammenschmelzens der
Partikel zu einem festen Bauteil, ist die Differenz der freien
Grenzflächenenergie zwischen Anfangs- und Endzustand. Die Mechanismen
des Differenzausgleichs bestehen bei homogenen Pulvern (d. h. einphasige
Systemen) aus der Reduzierung aller äußeren und inneren
Begrenzungsflächen. Zu den „äußeren Begrenzungssflächen“ gehört die
Außenkontur des Bauteils, sowie die Wände von außen zugänglichen Poren.
Im Gegensatz dazu fasst man die durch die Außenkontur eingeschlossenern
Porenoberflächen als „innere Oberflächen“ zusammen. Ein weiterer
grundlegender Antrieb des Sintervorgangs ist der Abbau von
Strukturdefekten durch die Umbildung des beim Spritzgiessen
geschlossenen mechanischen Pulververteilungskontaktes zu
Großwinkelkorngrenzen. Auf Grund der Vielzahl physikalischer Vorgänge
und Teilprozesse beim Sintern, die von Temperatur, Zeit sowie anderen
Einflussfaktoren abhängen, existiert keine geschlossene physikalische
Formel, die den Prozess als Ganzes zu beschreiben vermag. Daher ist es
aktuell nicht möglich vorab wissenschaftlich konkrete Voraussagen auf
die Eigenschaften der Sinterbauteile zu machen. Für die Praxis ist das
jedoch nicht immer erforderlich. Auch hier liegt, wie immer, das
Know-how bei dem Prozessanwender.
Die allgemeine Form des Sinterprozesses besteht aus einer
nichtisothermen Aufheizphase und einer anschließenden isothermen
Verweildauer bei Sintertemperatur. Anschließend wird das mehr oder
weniger dicht gesinterte Bauteil kontrolliert bei langsamer Abkühlrate
auf Raumtemperatur gebracht. Für Wärmebehandlungseffekte kann es
sinnvoll sein das Bauteil auch schnell Abkühlen zu lassen.
Entbindern

Es gibt unterschiedliche Arten des Entbinderns. Zum Entbindern muss der Grünling, also das Spritzgussteil, in den Entbinderungsofen gesetzt werden. Nach Ende dieses Vorgangs wird von einem Braunling gesprochen. Um den Braunling besser transportieren zu können wird in manchen Fällen ein Teil des Binders im Bauteil belassen. Es gibt also einen Unterschied zwischen dem Prozessschrittes Entbindern und dem Ende des Entbinderns. Während dem Sintern wird diese verbleibende organische Komponente aufgelöst und das Bauteil ist komplett entbindert.
Hier soll vorerst nur das thermische Entbindern vorgestellt werden. Beim thermischen Entbindern werden die Grünlinge in einem Ofen abgelegt und der Ofen wird definiert erhitzt. Dadurch zersetzt sich der organische Binder. Je nach Material sollte auf die Atmosphäre geachtet werden, damit keine chemischen Reaktionen beim Entbindern auftreten. Nach beendigung des Binderprozesses folgt der darauffolgende Schritt, dass Sintern.
9 Artikel (2 Seiten, 6 Artikel pro Seite)